Recognizing the Fundamentals and Applications of Plastic Extrusion in Modern Manufacturing
In the realm of contemporary production, the strategy of plastic extrusion plays an important duty. Unwinding the basics of this process reveals the true versatility and potential of plastic extrusion.
The Basics of Plastic Extrusion Refine
While it may appear complicated, the principles of the plastic extrusion process are based on fairly simple concepts. It is a manufacturing process in which plastic is thawed and then formed into a continuous account through a die. The raw plastic material, commonly in the type of pellets, is fed right into an extruder. Inside the extruder, the plastic is subjected to heat and pressure, triggering it to melt. The liquified plastic is after that required through a designed opening, known as a die, to form a long, constant item. The extruded item is cooled and after that cut to the desired length. The plastic extrusion process is extensively used in different markets as a result of its cost-effectiveness, versatility, and efficiency.
Various Sorts Of Plastic Extrusion Methods
Structure upon the basic understanding of the plastic extrusion procedure, it is essential to discover the various strategies involved in this manufacturing approach. The two primary strategies are profile extrusion and sheet extrusion. In account extrusion, plastic is melted and formed into a continual profile, typically made use of to produce pipelines, rods, rails, and home window frameworks. On the other hand, sheet extrusion produces large, level sheets of plastic, which are commonly more processed into items such as food packaging, shower curtains, and auto parts. Each technique needs specialized equipment and precise control over temperature and stress to guarantee the plastic keeps its shape throughout cooling. Recognizing these methods is crucial to utilizing plastic extrusion successfully in modern-day production.
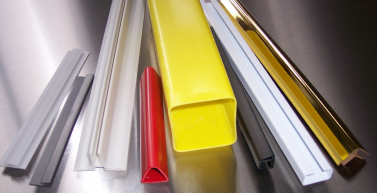
The Function of Plastic Extrusion in the Automotive Market
An overwhelming majority of parts in modern lorries are products of the plastic extrusion procedure. This process has changed the auto market, changing it into a more reliable, economical, and flexible production market. Plastic extrusion is mainly used in the manufacturing of different vehicle components such as bumpers, grills, door panels, and control panel trim. The process provides an attire, constant output, enabling producers to generate high-volume components with terrific precision and marginal waste. The lightness of the extruded plastic components contributes to the total reduction in automobile weight, improving gas efficiency. The toughness and resistance of these parts to heat, chilly, and impact enhance the durability of autos. Therefore, view website plastic extrusion plays a crucial role in automobile production.

Applications of Plastic Extrusion in Durable Goods Production
Past its considerable impact on the vehicle industry, plastic extrusion confirms similarly efficient in the realm of customer items producing. The versatility of plastic extrusion enables suppliers to develop and create intricate shapes and dimensions with high precision and effectiveness. The versatility, adaptability, see page and cost-effectiveness of plastic extrusion make it a preferred option for many consumer products suppliers, contributing substantially to the sector's growth and innovation.
Environmental Effect and Sustainability in Plastic Extrusion
The prevalent use of plastic extrusion in producing welcomes analysis of its ecological effects. Effective machinery reduces power use, while waste monitoring systems reuse scrap plastic, lowering raw product needs. In spite of these improvements, further innovation is needed to mitigate the ecological footprint of plastic extrusion.
Verdict
Finally, plastic extrusion plays a critical function in modern production, especially in the automobile and durable goods fields. Its versatility my response enables the manufacturing of a vast array of components with high accuracy. Its capacity for reusing and development of naturally degradable products provides an encouraging opportunity in the direction of lasting practices, consequently dealing with environmental worries. Understanding the essentials of this process is essential to maximizing its applications and benefits.
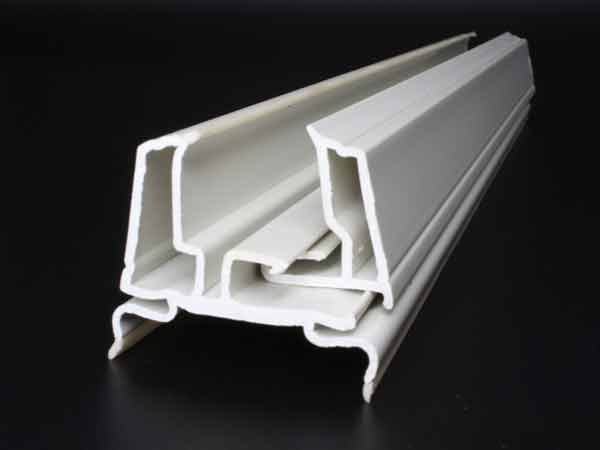
The plastic extrusion process is extensively used in various industries due to its flexibility, effectiveness, and cost-effectiveness.
Building upon the standard understanding of the plastic extrusion procedure, it is essential to check out the different methods included in this manufacturing technique. plastic extrusion. In comparison, sheet extrusion produces big, flat sheets of plastic, which are usually further refined into products such as food product packaging, shower drapes, and automobile components.A frustrating majority of components in modern-day lorries are items of the plastic extrusion procedure